With over 400 million tons of plastic produced per year and only a single-digit percentage of it being recycled, that’s a huge amount of potential plastic waste littering the ground and the ocean. And a bulk of that waste is single-use packaging.
One of the main benefits of a compostable material is that it can decompose and deteriorate faster in both controlled conditions and natural environments or ecosystems without human assistance.
The timescale of bioplastic packaging decomposition is measured in weeks or months as opposed to hundreds of years PET takes to dissolve. However, not all bioplastics are made equal, as some require specific environmental conditions to degrade quickly, such as high temperatures, consistent moisture levels, or exposure to industrial composting facilities that provide controlled conditions.
Besides looking for the most durable or effective plastic, it can be helpful to seek out material that degrades quickly. Let’s dive into the most common biodegradable plastics, how fast they can degrade, and why that matters.
What are the Fastest Biodegradable Materials
There isn’t a single set of rules on what constitutes a “fast” biodegradable material, such as hard cutoff points or distinct measures. But there are a few guidelines.
For example, a material can be considered fast to biodegrade if it completely disappears within months or a few years under ideal environmental conditions for decomposition.
This means that each material has a different set of requirements for decomposition or biodegradability. For example, wood degrades in a short time when left to rot in the open, indicating it’s biodegradable, but houses that use wood can last for several lifetimes.
A biodegradable material decomposes quickly in industrial, controlled conditions, usually between three to six months. These include a temperature between 50 and 60 degrees Celsius, adequate moisture levels, the presence of microbes that can process the biofilm (material that synthetic compostable materials are made from), and oxygen to feed them.
The process is different in natural ecosystems, such as landfills, soil, and marine environments. Under these conditions, a fast-biodegrading material should decompose within a few years, particularly if exposed to oxygen and sunlight.
Some materials (especially when considering food or medical applications) need to satisfy more stringent and regulated requirements and certifications to be called biodegradable. For example, EN 13432, like polylactic acid (PLA), is a European standard that dictates that packaging material mixed with waste mostly decays under commercial composting conditions within 12 weeks.
However, biodegradable materials require specific conditions to compost efficiently, highlighting the importance of commercial composting facilities. Explore how commercial composting plays a critical role in managing biodegradable waste, facilitating faster decomposition, and minimizing landfill use.
In general, so long as the material converts into natural elements swiftly and doesn’t leave toxic residue, and it does that in a timescale that its traditional counterpart (for the same purpose) can’t, it can be considered fast-biodegradable and fully compostable.
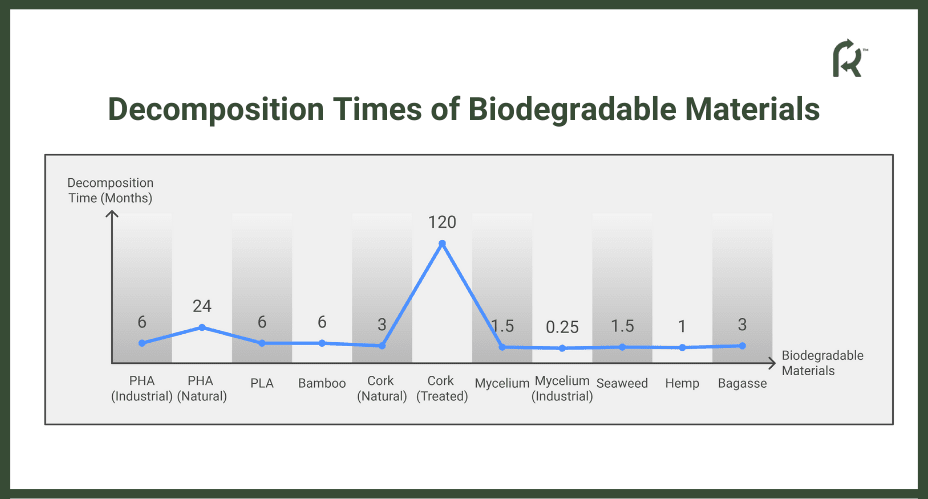
Overall, several biodegradable materials can satisfy some of these requirements:
- Polyhydroxyalkanoates (PHA): One of the most versatile biodegradable and compostable replacements for traditional plastics. Packaging made from PHA can compost in under six months in industrial settings, but it can also biodegrade within two to four years in natural ecosystems such as soil or marine environments.
- Polylactic acid (PLA): Another biodegradable and compostable plastic alternative that breaks down in high-temperature and moisture environments within six months.
- Bamboo: Some varieties can compost within four to six months and decompose in landfills within five years. Used as cutlery or as a wood replacement.
- Cork: Decomposes in natural environments within three to ten years, but natural cork can also compost within a few months (if not treated with sealants). Cork doesn’t have many packaging uses but has thermal insulation capacity.
- Mycelium (fungi): Can be a replacement for Styrofoam. Some niche products can biodegrade in as little as a month and a half and compost in industrial settings within a week.
- Seaweed: Used in food-safe or even edible packaging. Can compost in as little as six weeks.
- Hemp: Hemp-based plastic decomposes in ideal composting environments within weeks, up to a few months.
- Bagasse (Sugarcane Fiber): In ideal conditions (industrial composting facilities), this plastic replacement can decompose in under 90 days. Bagasse biodegrades in industrial composting facilities within 90 days under high temperatures (50-60°C), consistent moisture, proper aeration, and active microbial presence.
How Are Biodegradable Materials Useful?
Traditional plastics are made from fossil fuels and their byproducts. They do degrade over time, but they leave inorganic, toxic compounds and greenhouse gases while doing so, and their degradation rate is measured in decades or centuries. By contrast, compostable plastics decompose into water, carbon dioxide, and biomass, and they can do so at an accelerated rate.
As we go into the promising world of biodegradable materials, understanding their broader scope becomes essential. Learn more about the range of biodegradable materials that are shaping a more sustainable future, offering alternatives that lessen environmental impact and foster responsible consumption.
Here are some of the most common benefits of using them:
- Decreased plastic pollution: Bioplastics, being rapidly degradable, can have a profound impact on global plastic pollution. National Geographic estimates that 269,000 tons of plastic are floating in the ocean. Since some biodegradable plastic disintegrates in the presence of moisture, it has practically minimal impact on water-borne pollution, especially microplastics.
- Reduction of landfill waste: A Greenpeace report suggests that a vast majority of plastics go to landfills after they’ve been used, estimating roughly 44 million metric tons of plastic waste per year. Since biodegradable materials are highly reactive to microbes or the environment and can be actively used by the ecosystem they are in, their proliferation reduces the pressure created on landfills to store and process that waste.
- Lower carbon footprint: As mentioned, plastics are made from fossil fuel—which releases carbon dioxide—while biodegradable materials use naturally sourced options such as plant matter, sugars, or microbial matter. According to a 2017 study, corn-based plastics can reduce carbon footprint by up to 25%, which can be further increased when using renewable energy to produce it.
- Versatility: In essence, a biodegradable material doesn’t differ much from the one made from non-renewable resources. Typically, it will have similar physical properties, allowing it to be used for similar purposes as its non-renewable counterpart. All the while, it is recycled naturally by the environment and leaves no trace after a short period.
- Minimizes toxins in the environment: One of the biggest dangers of using traditional plastics is that they contain bisphenol A (BPA), a hormone disrupter that can negatively affect both humans and animals and is present in microplastics. A biodegradable alternative doesn’t degrade into BPA compounds and usually disappears without leaving harmful residues.
- Contributing to a circular economy: Since it can be recycled in composting facilities, a material’s constituent matter can potentially be reused, so the process of using and recycling the material emits minimal waste. This allows for an eco-friendly approach to producing and utilizing materials to extend their effective lifespan.
- Sustainability: Biodegradable materials are derived from renewable resources such as plants, agricultural byproducts, or microbial fermentation, ensuring a sustainable supply chain. Unlike traditional plastics that rely on finite fossil fuels, these materials promote sustainable practices by reducing reliance on non-renewable resources and supporting a greener, more regenerative production cycle.
With all these in mind, biodegradable materials have found significant uses throughout the world and across various industries, including:
- Biodegradable plastic that can be used as a food-safe packaging.
- Sustainable materials such as paper and bamboo replace plastic utensils and straws, particularly for single-use options.
- Takeout containers that can be made from food-safe biodegradable plastics that dissolve quickly in the environment.
- Farms that can use degradable mulch films, a material that also transforms into compost efficiently in the growing season.
- The cosmetic industry which can use lower carbon footprint packaging to reduce waste;
- Biodegradable trash bags that dissolve into the environment and allow compostables to be absorbed into the soil.
- Fishing nets can degrade, reducing the chance of leftover nets that harm animals and the environment.
PLA vs. PHA Biodegradable Materials
Two of the most promising bioplastics replacements that have already seen widespread use are PHA (Polyhydroxyalkanoates) and PLA (Polylactic Acid). These plastics are made from renewable or easy-to-source materials, making them ideal for large-scale production. Furthermore, their relative strength and durability make them versatile.
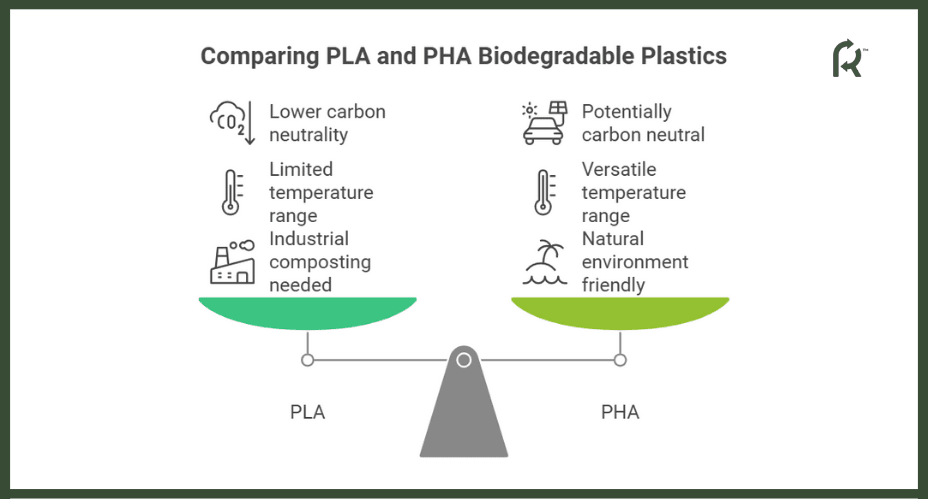
Let’s start with PLA:
- PLA is a polymer created by chaining lactic acid molecules (C3H6O3) together. As its name implies, the structure uses an ester bond between the constituent monomers.
- The ester bond can undergo hydrolytic degradation, so moisture and enzymes created by specific composting bacteria can dissolve it.
- Lactic acid has two enantiomers (D-LA and L-LA), which can be leveraged to create different properties in the resulting bioplastic. The ratio of left and right enantiomers affects how likely the structure crystallizes, which can change its physical properties, such as brittleness, transparency, and tensile strength, as well as how fast the material degrades.
- PLA is produced from fermenting biomass, mainly corn starch or sugarcane. This makes it an extremely renewable resource so long as the farms can produce the raw plants.
- Since its production is based on plant life rather than fossil fuel, it also has a much lower carbon footprint than traditional plastics.
- It’s used as a replacement for plastics across fields and industries, including food or cosmetics packaging and compostable containers, cutlery, medical injection aids, compostable bags, and mulch films, as well as in textiles and 3D printing.
PHA has a slightly different set of characteristics than:
PHA is a range of different polymers that has an O−CHR−CH2−CO base, where R can be a variety of compounds. One of the most common and basic types of PHA is polyhydroxybutyrate (PHB), where R is CH3.
- Similar to PLAs, PHAs have an ester bond between the monomers, which allows for hydrolytic degradation in certain conditions.
- PHAs are produced as energy-storage molecules during bacterial metabolism (i.e., these energy-storage molecules can be harnessed during bacterial fermentation). The bacterial “feedstock” can be plant oils, sugars, or even agricultural waste.
- Due to being made from fully renewable materials, PHAs are fully biodegradable and compostable which are easily absorbed into the environment.
- PHAs don’t necessarily require industrial conditions to compost or degrade.
- Some types of PHAs can even be carbon neutral by recycling carbon into the environment upon decomposition.
Here’s how PLA and PHA degradation compare and why PHA might be considered superior:
- PLA only quickly decomposes in industrial settings, with temperatures of over 60 degrees Celsius, allowing it to break down within three to six months. A 2017 study showed that PLA is practically inert at room temperatures and below. This makes it unsuitable for home-based or natural biodegradation.
- PHA decomposes in lower temperatures, allowing it to fully biodegrade quickly even without industrial composters, such as in soil or marine environments. For natural environments, the process can take roughly two years but can be expedited to a few months with increased temperature and bacterial enzyme content (such as in industrial settings). The ability to decompose at room temperature and in marine environments is practically unique among bioplastics.
How to Measure Biodegradability
The rate of degradation of organic and inorganic matter can be measured via a process called respirometry.
A standard respirometry test involves putting a sample of waste product (in this case, it would be the bioplastics or degradable material) in an enclosed container that houses soil and microbes capable of digesting it. Then, the mixture is aerated (i.e., oxygen is introduced to start the decomposition process).
At regular intervals, the sample is checked for the presence and concentration of CO2. Since carbon dioxide is present during the biodegradation and composting of practically all materials, as microbes that process the material expel CO2 as part of their metabolic processes, the concentration change over time is indicative of the amount of the sample that has decomposed.
ASTM D5338 (composting) and ISO 14855 are two standards that use this kind of testing. ASTM D5338 is a standard test method used to determine the aerobic biodegradability of plastic materials under controlled composting conditions. It measures the percentage of carbon in the sample converted to carbon dioxide by microbial activity, simulating industrial composting environments.
ISO 14855 is a similar standard test method designed to assess the ultimate aerobic biodegradability and disintegration of plastic materials under controlled composting conditions, providing results on the material’s decomposition performance over time.
Respirometry can also be done by measuring oxygen consumption in the sample. The environment and process can be the same as those for measuring CO2 levels.
One of the simpler tests for biodegradability is weight loss measurement. Unlike respirometry, the sample is not contained, but the CO2 and oxygen are allowed to leave containment. As the primary material decomposes into gases, its weight loss can indicate the rate of biodegradation.
Several factors influence the speed and rate of biodegradability:
- Temperature: Higher temperatures speed up decomposition. However, most materials typically also have a temperature benchmark, below which they won’t degrade much or at all (such as PLA, which doesn’t degrade until temperatures of upwards of 50 degrees Celsius). This is typically due to microorganisms such as bacteria and fungi that can process these materials but only start to thrive at those temperatures. In some compounds like PLA, higher temperatures start chemically breaking down the bonds between the molecules, speeding the process.
- Microbial presence and activity: Biodegradation primarily happens due to bacteria, fungi, and other microorganisms processing the material as its food. These organisms produce enzymes that are capable of dissolving the bonds between polymers or breaking down complex molecules into water and CO2. An environment with a variety of microbes is more conducive to decomposition, as partial byproducts can be used by other microbes to accelerate the process.
- Material structure and composition: Plastics made from renewable materials, such as PLA and PHA, have molecules that more rapidly degrade under the effect of certain enzymes, which can also be found in nature. However, PLA’s crystalline structure makes it more difficult to biodegrade without prior thermal processing, which is why it is unsuitable for degrading in natural environments.
- Sunlight exposure: Many materials can degrade when exposed to UV light, which jumpstarts the decomposition into water, CO2, or other compounds or breaks down the bonds between polymers. After that, microbial decomposition can fully process the material.
REGEN™’s Innovative Bioplastic Made from Renewable Resources
REGEN™ bioplastic is a PHA-type fully-degradable bioplastic made from natural materials that reduces to organic matter quickly. It’s fully compostable in both industrial facilities and natural environments, such as soil and marine habitats, which means it is absorbed by the ecosystem quickly and emits minimal waste. As such, it degrades much faster than other bioplastics such as PLA or bio-based PET.
The key innovation of REGEN™ is that it’s completely locally sourced and produced within Canada, streamlining the supply chain process and ensuring that local businesses can rely on the products to be available whenever they are needed.
Additionally, unlike traditional PHA production, REGEN™ is made from byproducts of the forestry industry, reducing the load and competition with agriculture and promoting a sustainable, circular economy.
REGEN™ bioplastic is completely non-toxic and transforms into compost efficiently, allowing it to be used in a variety of applications, including food, medicine, and cosmetics packaging, 3D printing, and toys.
Here are the benefits of partnering with REGEN™:
- The PHA bioplastic is made from completely sustainable and natural materials, minimizing the carbon footprint and supporting a circular economy.
- The bioplastic is as durable as traditional, petroleum-based plastics, yet it is more flexible than other bioplastics on the market, such as PLA.
- It creates a smooth finish, allowing it to be used for both decorative and practical items.
- The plastic is fully degradable in many kinds of environments, allowing brands to use it to raise their eco-consciousness and reach a wider audience.
- It can be used in a variety of applications, from earth-friendly packaging to toys and 3D printing.
- It’s sourced entirely in Canada, allowing brands to support the local economies.
Key Takeaways
- A “fast-biodegradable” material typically degrades in a matter of weeks or months, but some materials can take a few years to decompose completely.
- Unlike traditional plastics, modern bioplastics and renewable materials don’t leave toxic compounds or inorganic matter in landfills or marine environments.
- The compostability and biodegradability of materials depend on temperature, microbial conditions, oxygen presence, and the structure of the material, among other factors.
- PLA and PHA are some of the most biodegradable plastics.
- Due to its versatility and high rate of biodegradability, REGEN™ PHA plastics can be a superior choice for brands that want to push the image of eco-friendliness and future-oriented thinking.
Frequently Asked Questions
How Long Does It Take Biopolymers to Degrade?
Biopolymers can degrade in a few weeks to a few years. This depends on the soil composition, presence of moisture, temperature, exposure to sunlight, and the specific structure of the decomposing material.
What Is the Hardest Plastic to Degrade?
Traditional petroleum plastics, such as PET, can take thousands of years to fully degrade in natural environments, making them a menace to plastic pollution.
Which Are Degradable Biopolymers?
Two of the most versatile biodegradable polymers are PLA (polylactic acid) and PHA (polyhydroxyalkanoates). Others include cellulose, polycaprolactone (PCL), chitosan (derived from insect chitin), polybutylene succinate (PBS – made from sugar or starch), alginate, and polyglycolic acid.