Plastic pollution has become one of the most widespread environmental problems, and it typically is mentioned in tandem with carbon emissions and waste mismanagement directives.
Over the past few decades, many alternatives have been proposed to reduce the environmental and societal impact of single-use fossil fuel-based (petroleum and coal) plastics. To gauge their effectiveness, we can discuss sustainability in terms of degradation rate and speed, toxicity, carbon emissions, energy efficiency, renewability, and recyclability or compostability.
Unfortunately, many alternatives end up not checking all of these boxes or only doing so under very stringent or limited conditions. Here are some of the most commonly proposed alternatives to plastics.
Compostable plastics | A subtype of bio-based plastics that decomposes quickly in composting or industrial environments, such as PHA bioplastics. |
Stainless Steel | Fully recyclable and already used in a variety of industries. Stainless steel can replace plastics for long-term products such as packaging or storage. |
Glass | Fully recyclable and made from sand, glass is non-toxic and has significant industry use. It’s already used for food containers and other storage. |
Bamboo | Grows incredibly quickly and is fully sourced from natural materials. Can replace plastics in niche products such as cutlery, furniture, or toothbrushes. |
Bio-based plastics | Plastics are made from processes that primarily use plant matter and microorganisms. It creates a more sustainable production process but can be expensive to produce due to competing with food and feed. |
Coconut | Coconut is sustainably made and can be broken down into durable fibers, which can be used as plastic-like composites or even wood imitations. |
Recycled Paper or Cardboard | Paper and cardboard production are already incredibly high, and the natural biodegradability and recyclability of these products mean they can be incredibly sustainable. These can be made with agricultural residue, such as straw or husks. |
Upcycling Tires | Tires are incredibly durable and don’t naturally decompose. However, once they are no longer road-safe, they can be cut up and upcycled into furniture or similar products. |
Cork | Cork is grown fully sustainably from tree bark and can be readily recycled. It’s naturally resistant to bacteria and mold and can be used for manufacturing a variety of items. |
Are All Plastics Bad?
Contrary to popular belief, plastics aren’t exactly the be-all-end-all of pollution and environmental failure. In general, though, its environmental costs outweigh its benefits:
- Producing new plastics is considered to comprise 5% of global CO2 and carbon emissions.
- Many new plastics use coal for energy requirements, making the entire production process incredibly inefficient and environmentally unfriendly.
- PET and other types of commonly used plastics contain a hormone disruptor called bisphenol A (BPA). BPA microplastics can have long-term negative effects on animal life due to consistent exposure, including humans.
- Despite ongoing promotions of recycling oil-based plastics, only between 9% and 16% of all plastics are recycled. This creates significant pressure on landfills, where plastics degrade for hundreds of years.
- A significant portion of plastic waste ends up in the ocean. If the trend continues, UNESCO estimates the amount of plastic in the water will outweigh all the fish by 2050.
- Petroleum-based plastic does degrade, but not fully. That leaves small particulates, called microplastics, floating in the ocean or immersed in the soil. Microplastics have been linked with toxicity for the nervous, gastrointestinal, and immune systems in animals.
- To combat these effects, bioplastics (plastics from natural ingredients, typically biomass and microorganisms) have been proposed to have a much better environmental effect in terms of waste reduction and overall carbon footprint.
However, despite promising early results in synthesizing bioplastics, conventional plastics still have some benefits. The production process for most bioplastics involves the same feedstock used for animals, putting more pressure on agriculture and possibly endangering natural habitats to make more room for farms.
The necessity to grow plants to use for plastics also creates additional energy and resource requirements (particularly electricity, water, and soil). When comparing traditional, petroleum-based plastics and bioplastics such as PLA, some bioplastic products can require more than double the energy.
Worse yet, the feedstock for bioplastic material typically needs to be outsourced, which increases supply chain and logistics complexity. An alternative option, such as plastic from seaweed, has stringent collection requirements and needs to be transported inland.
This all leads to an increased carbon footprint. A study by Michigan Tech concluded that bioplastic straws have twice the carbon footprint of traditional ones.
What does this all mean? A truly renewable bioplastic material that reduces environmental impact and helps achieve the sustainability goals of large corporations is beyond our current capacities.
However, that doesn’t mean that brands can’t make small differences by using alternative materials at a smaller scale and supporting local businesses, a process that encourages responsible consumption.
Seaweed offers a compelling alternative for creating bioplastics, yet its collection and transportation pose unique challenges. Dive deeper into the process and benefits of creating plastic from seaweed, an innovative approach that promises to revolutionize the material landscape with minimal environmental footprint.
Top Sustainable Alternatives to Oil-Based Plastic
Now that you know the dangers of petroleum-based plastics and the large-scale inefficiencies of using bioplastic alternatives, let’s see which materials show the most promise when it comes to eliminating or minimizing plastic use:
- Glass: Glass is made from sand in an energy-efficient and renewable process. Furthermore, glass is more easily recyclable, but perhaps most importantly, the material is practically inert for most chemical elements. Glass is naturally reusable and supports waste reduction by promoting healthier spending habits.
- Stainless steel: Stainless steel is 100% recyclable, meaning that anything made from it can eventually be smelted back into steel, and the composites of steel are valuable enough to be recovered from old steel products. According to U.K. statistics, 60% of stainless-steel products are made from recycled steel.
- Bamboo: Bamboo is one of the fastest-growing trees in the world, reaching a mature size in a few months. Additionally, bamboo cultivation doesn’t require pesticides, lowering bamboo farming’s impact on the environment. Products made from bamboo can decompose in composting conditions since they typically use minimally processed fiber that rots in microbial-rich environments.
- Compostable plastics: Biodegradable plastics can be made from a variety of materials, typically plant matter, biomass, or byproducts of microbial metabolism, such as lactic acid. Since bioplastics like polyhydroxyalkanoates (PHA) are made primarily from natural resources, they degrade into water, carbon dioxide, and organic matter, leaving no toxic residue or chemicals in the soil or water. However, it should be noted that not all biodegradable plastics are completely additive-free, and some take decades to biodegrade in natural environments.
- Bio-based plastics: Bio-based plastics can be fully or partially made from natural resources, but the result has the same molecular structure as traditional petroleum plastics. However, the more energy-intensive and mutable production process might make the plastic unable to degrade back into its constituent parts via composting and significantly prolong its biodegradability timeline, just like in traditional plastics.
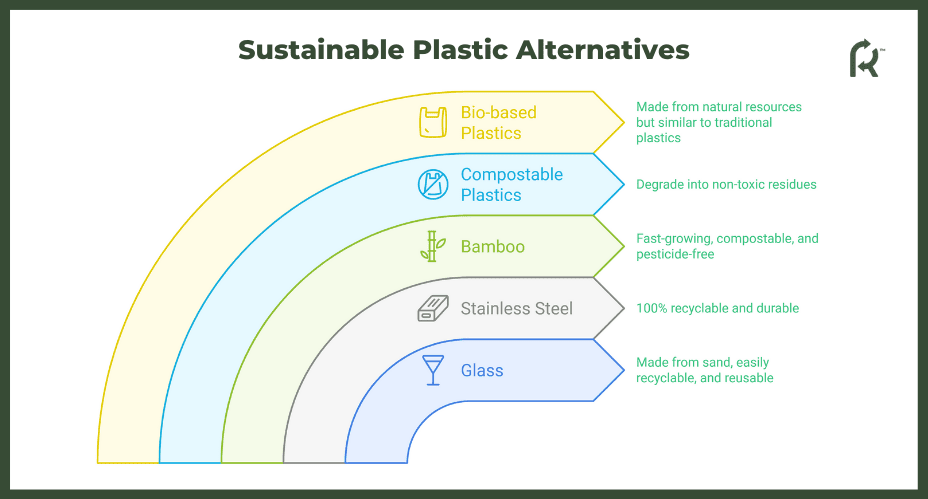
Out of these alternatives, glass and stainless steel have perhaps the most market potential and penetration. Since these materials are already used worldwide and can be fully recycled, they are also sustainable and minimize waste accumulation.
Furthermore, glass and stainless-steel products already exist in many spheres that plastics now occupy (such as food packaging and storage). However, they are designed for long-term applications rather than single-use, which is the main issue with plastic waste. Therefore, they occupy slightly different niches that can’t be directly compared.
Bamboo, while being plentiful in optimal conditions, still requires labor-intensive processing. Furthermore, bamboo doesn’t grow in all environments (being largely limited to Asia), making it more expensive to produce and transport to the Western world.
On the plus side, bamboo has become increasingly popular for sustainable cutlery, furniture, and toothbrushes. However, this is still largely a niche industry, with the bamboo market reaching only $69 million in market value in 2022.
Bio-based plastics, whether they are biodegradable or not, help remove some of the toxic waste products associated with oil-based plastic use. However, producing these plastics in large enough quantities to overtake petroleum plastics is currently beyond most industrial capacities.
Bio-based products run into the problem of needing large quantities of resources to produce (mainly water, land, and energy) that all compete with food and feed production. This means that ongoing research to improve the scalability and supply chains of these products will directly improve their cost-effectiveness and sustainability.
As we continue to search for sustainable alternatives that minimize waste, the development of eco-friendly packaging becomes increasingly pertinent. Learn more about cutting-edge eco-friendly packaging solutions that not only reduce environmental impact but also offer practical benefits to consumers and businesses alike.
PHA (Polyhydroxyalkanoates)
PHA is a compostable and rapidly biodegradable plastic that has gained significant improvement and interest in recent years. Made from byproducts of bacterial fermentation of biomatter (including waste), PHA is one of the few fully natural bio-plastics that is capable of decomposing entirely at room temperature and in marine environments.
It also exhibits an excellent combination of flexibility and strength, allowing it to be used in both industrial and commercial applications, such as food packaging, medical devices, toys, or even as a 3D printing filament. This makes it superior to other bio-based plastic alternatives, as it directly contributes to a circular environment and has a lower carbon footprint.
Here’s how PHA differs from traditional PET plastic:
- Since it’s made from naturally sourced materials, the plastic is free from harmful chemicals that would leach into soil and water during the degradation of traditional plastic.
- PHA can degrade in industrial conditions (temperatures above 50 degrees Celsius and sufficient soil and microbial content) and commercial compostable solutions in as little as three months.
- Unlike PET, PHA decomposes naturally in marine environments within one to two years. It degrades into water, carbon dioxide, and biomass, which conserves natural resources.
- Creating PHA supports a circular economy since the product is entirely made from natural materials that can be reused, recycled, or composted.
PHA’s ability to degrade in a range of environments underscores the importance of scalable composting solutions. To better understand how these materials can be integrated into commercial operations, explore innovative commercial compostable solutions that are redefining waste management practices and helping businesses achieve sustainability goals.
PLA (Polylactic Acid)
PLA, or polylactic acid, is bio-plastic derived from plant matter such as corn starch or sugar cane. Since the product is made from natural resources, it’s a more sustainable and eco-friendly variation of traditional plastics.
Here are some of the benefits of using PLA instead of traditional oil-based plastics:
- Since it’s made from sugar or corn starch, the production process uses fewer fossil fuels and more renewable materials.
- PLA has a higher temperature resistance than other bioplastic options and doesn’t degrade at room temperature.
- PLA degrades in industrial conditions (high temperature, moisture, and microbial content) within three to six months.
- Due to its high strength and durability, it has a wide range of applications, including food and medical packaging, 3D printing, cutlery, and other consumer goods.
- This allows it to compete with PET plastics for single-use applications.
Starch-based Plastics
Starch-based plastics are bioplastics that can be derived from a wide variety of plant matter, such as corn, potato, or wheat. Due to the incredible abundance of these resources, creating starch-based plastics is more sustainable than using petroleum-based products.
However, it should be noted that this directly competes with food and feed production for humans and animals, so its spread can be limited.
Here are some of the best benefits of these plastics:
- Starch-based plastics readily compost under industrial conditions. Since they’re made from starch, the process degrades them into water, carbon dioxide, and traces of biomatter, leaving practically no trace elements.
- This type of bio-plastic can be blended with other bio-plastics to improve its heat resistance and general durability. The resulting product can typically biodegrade as well.
- Starch-based plastics are relatively less expensive to produce than other bio-based plastic types. From 2015 to 2020, these plastics made up the largest share of the bioplastics market.
- They can be used in a variety of applications, from single-use recyclable bags or loose-fill packaging to phone cases.
Bio-based PET
Bio-based PET is a blend of traditional petroleum-based plastics and naturally sourced materials, designed to behave similarly to traditional PET plastic as possible. The “bio” portion is derived from sugar cane. Much like traditional plastics, bio-based PET is strong, durable, and doesn’t degrade or decompose.
More modern bio-based plastics have a higher percentage of their PET content made from natural materials, contributing to improving sustainability in creating the material. Here’s how bio-based PET stacks up against its petroleum cousin:
- Like traditional PET, bio-based PET doesn’t compost or degrade naturally. This makes it less eco-friendly than alternatives such as PLA or PHA.
- Some bio-based PET materials have as little as 30% of their supply sourced from renewable resources.
- Bio-based PET is perhaps most famously used in bottles or food containers. The Coca-Cola company announced in 2021 that it would move towards 100% bio-based PET for its plastic packaging.
How Is PHA Different from ‘Corn-Plastics’?
PLA (commonly known as corn plastics since it can be derived from corn starch) and PHA are perhaps two of the most promising alternatives to traditional plastics.
PLA is made from sugar-rich plant matter (corn starch, sugar cane, cassava) that is left alone to allow for bacterial fermentation to create lactic acid, which is then chemically polymerized to create a durable plastic.
On the other hand, PHA is created from byproducts of microbial metabolism, which is extracted from bacteria that are fed excess feed (which can be plant matter or waste products). The PHA is then chemically processed and purified to create granules that can be used to create plastics.
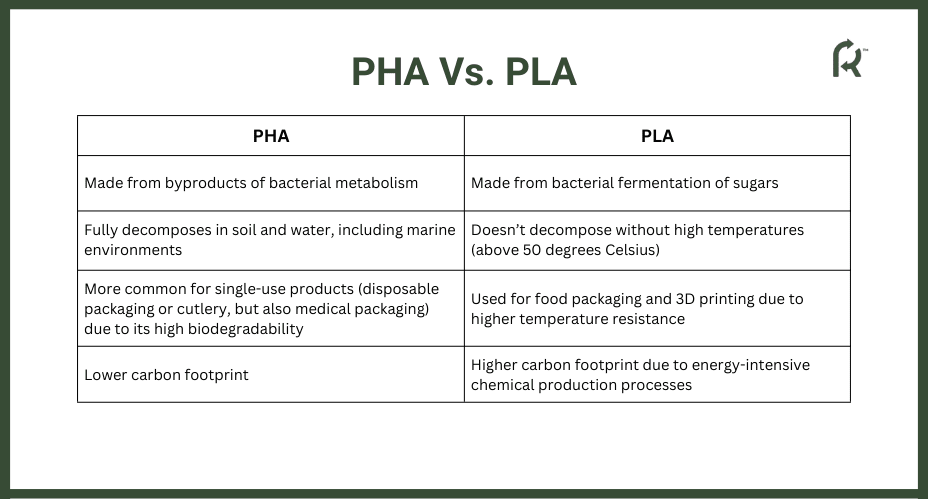
Here’s how they compare:
BOSK Bioproducts’ Pioneering Plastic Pollution Solutions
BOSK Bioproducts creates PHA-based bioplastics that go a step further into ensuring sustainability and eco-friendliness. Our REGEN™ is a ready-to-use, fully compostable, and biodegradable plastic resin for your next eco-friendly package design. Here’s what you need to know:
- Rather than using traditional raw plant matter, BOSK uses biofilm and plant matter from forestry industry renewables, reducing the plastic’s overall carbon footprint and tapping into underutilized resources that would be left to waste.
- BOSK sources all of its materials within Canada, streamlining the supply chain and minimizing transportation costs.
- REGEN™ supports a circular economy by utilizing byproducts of other industries that are no longer used rather than competing with agriculture (as with traditional bio-based plastic manufacturing).
- Much like PHAs, REGEN™ is fully biodegradable in both soil and water, including marine environments. The plastic degrades into water, carbon dioxide, and organic matter that is safe for the environment and can be processed by the ecosystem.
Key Takeaways
- There are two main types of bio-based plastic alternatives, but PHA offers the best combination of durability, versatility, and fast biodegradability.
- Stainless steel and glass are materials that can be used as long-term plastic replacements to try to transform consumer behavior.
- Bioplastics have tremendous potential to replace traditional PET due to their higher rate of industrial or natural compostability.
- Despite improvements in the industry, PET plastic is highly efficient to produce, and some bio-based plastics end up having a larger carbon footprint and energy requirement.
Frequently Asked Questions
What Material Will Replace Plastic?
There’s still a bit of uncertainty on the best plastic replacement. Glass or stainless steel are excellent recyclable materials that promote shifting consumer behavior, but only work in specific niches. Bio-based plastics can be used for single-use applications (much like traditional plastics), but supply chains for these materials aren’t fully developed to reach full market penetration.
Is There a Sustainable Plastic?
Plastics can be made more sustainable by utilizing bio-based materials such as corn starch, sugar cane, or other plant-based products, or byproducts of other industries to produce materials that behave similarly to traditional PET plastic. However, one of the big challenges in creating sustainable plastic is balancing plastic production and agricultural use.
Is There Renewable Plastic?
Renewable plastics can be readily recycled either into the industry or the ecosystem. This can be done by chemically reverting the plastic to its constituent and combining it with new bioplastic, or composting the plastic to create feed that can be used for future plastic production.